Technical Newsletter
Issue 29
Upgrading an Old Office Plaza
Braemar Ridge Office Plaza was starting to show its age. The new owners were looking to add new life into the building and the site in order to attract new clients as well as hold on to the ones they already had. The exterior rehabilitation was straight forward. The building was cleaned and refaced with aluminum fascia, new windows, and new sidewalks. But the site work was more complicated. The building was first built in the mid-seventies on a somewhat hilly site which required retaining walls. In the seventies, wood timber walls were very popular and the original site construction used many. Over the years, many of the deteriorating wood walls were replaced. Unfortunately, not all at once which resulted in a variety of different segmental retaining walls being used creating an inconsistency in the site esthetics. To this date, a few wood walls also still remain. Therefore the current site was a mess of varied wall conditions and looks.
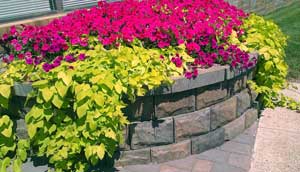
The owners sought out the assistance of Allan Block Corporation, who they have worked with on other properties, as well as their local manufacturer, Amcon Block and Precast of St Cloud, MN to find a solution for the site. Together with the design assistance of Ron Vickery of Vickery Engineering and the experience of Harris Construction, the site review and planning started. It was quickly determined that due to either space requirements or size of wall being replaced, that each wall would require a different design and construction process. The owners reviewed all of the block choices and quickly decided on Allan Block Fieldstone for its incredible aesthetics and versatility to fit the design and construction specifications because their goal was to bring a common look to the site.
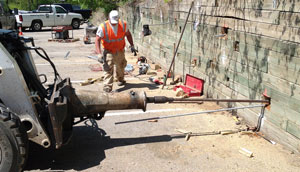
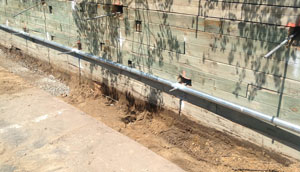
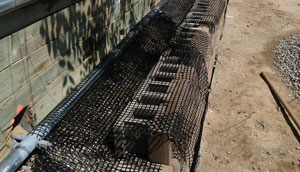
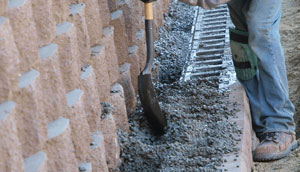
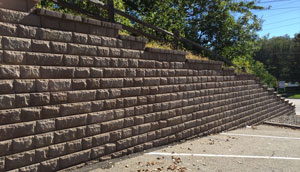
The site had a number of smaller landscape size walls, as well as three larger walls to replace. The AB Fieldstone with its optional short or long anchoring units would easily work for any of the final wall conditions. Vickery Engineering utilized this versatility in their designs because the lists of wall design requirements were long. The tallest wall would remain in place due to the limited excavations space and the AB Fieldstone would be built in front of the existing wall and attached using no-fines concrete. The second tallest wall would be removed entirely and replaced with an AB Fieldstone geogrid reinforced wall and the last of the engineered wall was a taller wood wall that AB Fieldstone would be used to reface using soil nails through the old wall to anchor the new facing. Braemar Ridge is a relatively small site with more design and construction varieties then most other larger projects ever have. Vickery Engineering and AB Fieldstone made this complicated site a success and a highly sought after location for local businesses.
Variations on Design
For Braemar Ridge, Vickery Engineering used the AB Walls Design Software to design all of the walls that required geogrid reinforcement or No-Fines Concrete. With the variations of the wall types they also needed to design a soil nails application.
Vickery did hand calculations for the walls requiring soil nails through the face of the wood timber walls. The soil nail wall designs required three things; the on-center spacing of the nails (both horizontally and vertically), and the diameter and length of the spreader bar. Once the nail spacing was determined, the horizontal force on the spreader bar could be determined based on active earth pressure and surcharge forces on the wall facing. Because the wood wall was in sound condition the number of nails were based more on the pipe size than the need for support. Vickery designed the wall to have about 24 in. (600 mm) of working space between the wood wall and the back of the block. This allowed space for the installer to work with the grid and spreader bars and leave room for placing and compacting wall rock. There are a few ways to connect the facing to the spreader bar, but Vickery chose the most common way of placing grid between the lower courses and bringing it up around the back of the pipe and back to the wall between the next two courses above.
The large 20 ft. (6.1 m) SRW wall that the owners wanted to update was the next challenge. Because the wall was a segmental wall, the individual units could have been unstacked; leaving the geogrid layers in place and then restacked using the new AB Fieldstone units by reconnecting the grid as the wall is reconstructed. This is a complicated process for the installers and takes great care to not damage the in-place geogrid during dismantling of the old wall. Vickery and the owners decided to sacrifice the old wall by leaving it in place and building the new AB Fieldstone wall in front of it. There are a few ways of doing this but space in front of the wall was not overabundant. It was suggested to build the new walls with about 6 in. (150 mm) of clearance between the face of the old wall and the back of the AB Fieldstone unit then fill the cores and void with no-fines concrete. The no-fines concrete would adhere to the split-face of the old wall and solidify in the voids of the AB Fieldstone short anchoring units, thus making a continuous solid connection between the new and old walls.
Versatility of AB Fieldstone
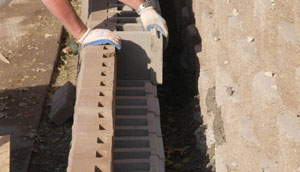
While the AB Fieldstone is perfect for standard gravity and geogrid designed wall projects, the Braemar Ridge project was perfect to illustrate the versatility of the AB Fieldstone system. These two piece units install fast and easy due to the lighter weight of the individual pieces. The fact that the system can use either the standard short anchoring units or the long anchoring units for taller gravity walls is one of the keys to its versatility. The created hollow core is another. Like all the other Allan Block products the hollow core provides a continuous rock-lock connection to geogrid, additional attachment locations for no-fines concrete applications, a path for vertical reinforcing bars in cantilever masonry applications and finally a secondary drainage path for incidental waters that may pass through the systems. Also, The facing units come in a variety of facing textures and lengths providing the owners a nice variety of looks. At Braemar, Harris Construction was able to AB Fieldstone in gravity, geogrid, soil nail and no-fines applications.
What Makes Retaining Walls Work
Retaining walls are typically built and used to hold back soil for many different types of applications. The size of the actual retaining wall unit is important. With a larger block footprint a taller gravity wall can be built that can safely retain the pressure from the soil behind it. The short anchoring unit (SAU) with either facing unit develops a block assembly that is approximately 13 inches (325 mm) deep. The long anchoring unit (LAU) with either facing unit develops a block assembly that is approximately 24 inches (600 mm) deep. Use the following general guidelines to determine which anchoring unit is most appropriate.
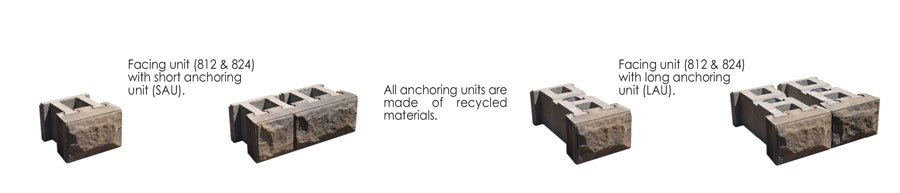
- The short anchoring unit (SAU) is used for lower height gravity walls and reinforced walls.
- The long anchoring unit (LAU) may provide the solution for projects that require taller gravity wall heights where space is limited behind the wall by property lines, right of way issues, underground utilities or existing structures.