Technical Newsletter
Issue 2
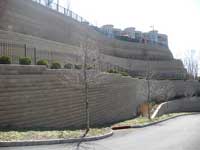
The Skyline Ridge Development is a large residential community in Springfield, New Jersey with 90 luxury condominiums
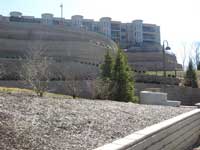
Project Information
Name:Skyline Ridge
Springfield, NJ
Product:AB Classic
Certified Allan Block Contractor:
Pillari, LLC.
Allan Block Manufacturer:
Clayton Block - Edison, New Jersey
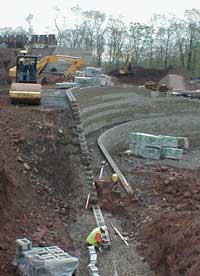
Preconstruction meetings are important because it makes sure you have the opportunity to communicate the project’s scope of work.
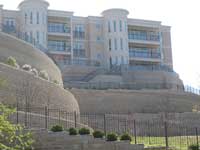
Regularly scheduled construction meetings help to keep lines of communication open and are a good way to solve problems that might arise.
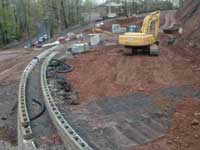
For more information on designing your tall wall, and to get your AB Walls Software Tall Wall Password, contact the
Allan Block Engineering Dept
engineering@allanblock.com
(800) 899-5309
Attention is Needed When Building Taller Retaining Walls
The Skyline Ridge Development is a large residential community in Springfield, New Jersey with 90 luxury condominiums. The original site was very hilly and provided no quality space for the building structures. The solution was a series of large Allan Block walls built to form a construction plateau allowing the condos to overlook the Manhattan skyline. The project has 17 Allan Block walls consisting of more than 75,000 AB Classic block and a maximum grade change of 70 ft (21.3 m).
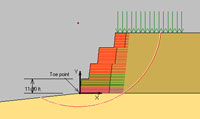
Tall walls such as these require a very high level of analysis during design and continuous inspections for compaction and soil quality during construction. Porcello Engineering of Pine Brook, New Jersey, used AB Walls Design Software for the initial design of the individual Allan Block walls and ReSSA to analyze the global stability of the terraces and the entire site. These walls were not only designed to support parking and recreational areas, but the building structures were founded on spread footings built directly above the wall’s reinforced soil mass. Therefore, minimizing future settlements was given the highest level of importance in design and construction. Fortunately, the site soils consisted of high quality granular material, perfect for design and construction.
To ensure that construction went smoothly, Porcello and the general contractor first held a preconstruction meeting to bring all the parties together and to set a workable schedule. During construction they held weekly site meetings to discuss the progress and quality of construction. Another thing Porcello and the GC insisted on was an on-site soils engineer to monitor soil quality and compaction levels. Detailed inspection logs were kept and reviewed at each weekly meeting allowing for a seamless building process.
For a further discussion on Skyline Ridge and other Allan Block projects see the case study section of our site.
Meeting Your Way to a Successful Retaining Wall Project
When building a large retaining wall, it is not just about having the proper equipment and installation knowledge. Yes, these are critical elements and the crews of Pillari LLC., are AB Certified Installers, but good communication is as equally important.
Communication between all involved parties helped ensure the successful project completion at the SkylineRidge Development. It started with a preconstruction meeting and included regular scheduled construction meetings throughout the project. These meetings must be applied for large walls, but should be a consideration for all wall projects.
Preconstruction meetings are important because it makes sure you have the opportunity to communicate the project’s scope of work.
Who should attend the meetings?
- Owner or Owner’s Representative
- Site Engineer
- Wall Designer
- Geotechnical and Testing Engineers
- General Contractor
- Wall Installer
- Other Subcontractors (utilities, irrigation, paving, landscaping etc...)
This meeting should cover the items listed below, but a more complete list can be found on the Construction and Inspection Checklist within our AB Commercial Retaining Wall Manual.
- Job costs and schedule
- Review wall design and compliance to current site drawings
- Verification of site soils
- Water management activities during and after construction
- Material staging and delivery schedule
- Outline project responsibilities and testing requirements
Regularly scheduled construction meetings help to keep lines of communication open and are a good way to solve problems that might arise. If the site engineer, wall designer, general contractor and wall builder are all effectively communicating, project schedules and costs are kept in sync.
Special Considerations When Designing Taller Walls
The task of designing a wall system like the one at the Skyline Ridge development can seem overwhelming. Project success on this type of wall is not only defined as the wall being built safely, on time, and within budget, but it must also stand the tests of time. Take into account the structures being built on top of this mountain of Allan Block and the risks of properly designing and constructing these walls are magnified. To ensure success on any project, but especially tall walls like these, consider the following key items during the preparation of your construction documents:
- Qualified Contractors – Consider adding a minimum experience level to your construction documents, stressing the importance of a certified contractor with prior job references.
- Detailed Plan Review – Provide a careful review of the site geometry, structures above the wall, and structures below the wall to resolve any potential issues or construction conflicts.
- Water Management – A detailed review and implementation of a water management plan is essential. This should include identifying the above and below grade drainage, along with utilities such as storm drains, curbs and gutters to evaluate their effect on the wall performance.
- Increase Compaction Requirements – Consider compacting to a level higher than 95-percent of Standard Proctor to minimize future settlements, one of the keys to tall wall projects.
- Onsite Inspection – Provide detailed requirements for onsite inspection to ensure the wall is complying with your specifications. A detailed construction log should be signed-off at incremental levels and preserved with the project records.
- Use Select Fill – Consider using imported select fill consisting of compactable sandy gravel with a plasticity index (PI) of zero for the bottom one third to one half of the wall for the entire depth of the reinforced soil mass.
- Bench Cutting Slope – A long sloped cut can create a slip surface behind the wall. Consider making a series of benches in the slope to disrupt this continuous slope.
Keeping these few items in mind while generating your construction documents will help make your project a success for everyone involved. For more information on designing your tall wall, and to get your AB Walls Software Tall Wall Password, contact the Allan Block Engineering Department at (800) 899-5309 or by e-mail at engineering@allanblock.com.
Helping you go Green
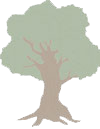
Did you know that one of the LEED® credits for Sustainable Sites is Stormwater Design: Quantity Control (SS Credit 6.1)? One of the major components of storm water management is quantity control, particularly in newly developed areas where open space is replaced by buildings, parking lots, roads and other impervious surfaces.
The most common method for maintaining pre-development runoff conditions is through the use of a detention pond or other on-site storage. A detention pond captures flow and releases it slowly over time, thereby decreasing peak flows and associated flooding problems.
Using Allan Block Retaining walls to construct the banks of the detention pond is a simple and effective solution, which allows you to control both the water quantity and conserve space. Check us out for a detailed description of how Allan Block products can help your project achieve LEED® credits.