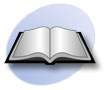
Print Case Study
Project Information
Name: Woodland Heights
Chaska, Minnesota
Product: AB Classic
Size: 1400 ft² (130 m²) 8 ft (2.4 m) maximum height
Local Engineer: Duffy Engineering and Assoc. Inc.
General Contractor & Wall Builder: The Lawn Ranger Incorporated
Allan Block Manufacturer:
Amcon Block - Saint Cloud, Minnesota
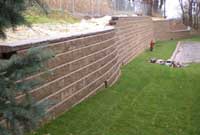
The retaining wall is located on the down slope side of a farm field, approximately 3 ft (1 m) from the property line
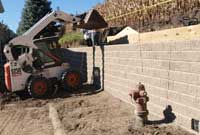
Existing water utilities and property lines meant using No-Fines Concrete to solve the reinformcement problem
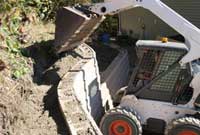
Construction was done in phases to prevent the entire site from being under construction at one time
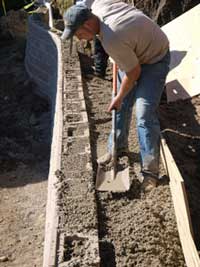
Retaining Walls Built in Tight Places
Woodland Heights is a multifamily development built in the 1980s on a hillside overlooking the City of Chaska, Minnesota. Like many suburbs of the Minneapolis/St. Paul metro area, this project was developed on former farmlands. In this particular case, actively cultivated farmlands are still adjacent to the townhomes. An Allan Block retaining wall was proposed to replace an existing failing wood wall along this property line. This wall was to be located on the down slope side one of these farm fields, approximately 3 ft (1 m) from the property line. In addition to the tight site conditions, the new retaining wall must also endure seasonal drainage from the field runoff, northern climate freeze-thaw cycles, permanent obstacles in front of the wall, potential surcharges above the wall, and withstand the test of time. This wall was to solve all the problems that the two prior wood retaining walls had failed to do.
Design
The new block retaining wall needed to have as small of a footprint as possible to avoid conflicts both in front of the wall and behind the wall. For this project an easement was not possible behind the wall to place geogrid, and moving the existing water utilities would be cost prohibitive. To solve this problem, Duffy Engineering and Associates designed the retaining wall using No-Fines Concrete as the backfill material.
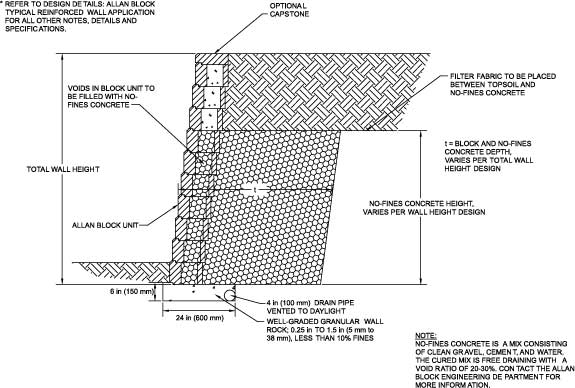
No-Fines Concrete
No-fines concrete has been in the industry for over 15-years and is used extensively in various parts of the world. Unlike other concrete mixes, it is made from only the Portland cement and coarse aggregate; it does not use the sand (fine aggregate) in the mix design. This allows voids to develop within the concrete mass that would otherwise be occupied by the sand. Once fully cured, this concrete mass becomes very stout, but permeable. With the addition of all these interconnected voids, water drains through the mass better than that of most backfill and native soils.
From a purely design standpoint, the no-fines concrete combines with the Allan Block facing to form a larger gravity wall. Just like any other gravity wall system, it needs to be heavy enough to resist typical sliding and overturning forces plus the solidness of the system forms a natural barrier against internal sliding. Internal sliding is one of the many design checks built into an Internal Compound Stability (ICS) analysis.
Construction
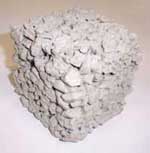
No-Fines Cube Example
After receiving approval from the city and all the utilities were marked, construction activities began. The Lawn Ranger Inc. planned their construction activities in a series of phases to prevent the entire site from being under construction at the same time. This turned out to be a good decision because the following day the site received 4 inches (100 mm) of rain within 2 days. Fortunately, The Lawn Ranger used good water management practices by planning ahead and covering the entire site with large tarps.
The first section of the wall constructed was a gravity wall near the townhouse foundation, followed by disassembly of the 8 ft (2.4 m) failing wood wall. Since the footprint of the no-fines concrete retaining wall was smaller than that of a geogrid reinforced wall, the expense of hauling the excavated soil offsite was minimized. After installing the first two courses of block, a technical sales representative from Amcon Block and Precast stopped out on the jobsite to assisting with the installation of the no-fines concrete backfill. With this additional expertise, the learning curve was greatly reduced and the crew worked quickly and efficiently to fill the block cores and the required 2.5 ft (0.76 m) behind the block retaining wall with the permeable concrete. Once these two courses were backfilled, the next two courses were installed. By this time, the first lift of concrete had cured enough to place the next lift of concrete. This process was repeated until the top of the wall was reached. In the end, 40 cubic yards (30.6 cubic meters) were placed within this retaining wall structure. Stacking two courses at a time is acceptable when using no-fines concrete if the installer are careful to work the concrete into the cores of both course the block.