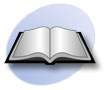
Print Case Study
Project Information
Name: Progress Quarry
Beaverton, Oregon
Product: AB Collection & AB Courtyard Collection
Size: Over 30 Walls in two phases Approx 44,000 ft² (13411 m²) Ranging in height up to a 27 ft (8.23 m) maximum height
Local Engineer: ABHT Structural Engineers
General Contractor & Wall Builder: Bones Construction & Darkhorse Construction
Allan Block Manufacturer:
Oregon Block - Prineville, OR
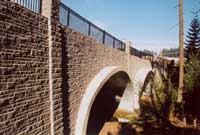
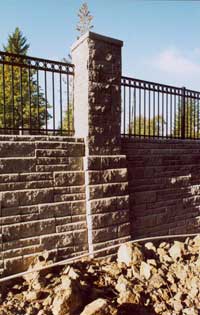
Figure 1: Pillar within the Wall Fence
Figure 4: Bridge Wall Construction
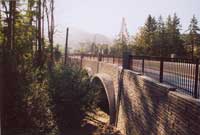
Retaining Walls Add Beauty to Commercial Project in Residential Setting
The Progress Quarry Development project in Beaverton, Oregon was a large scale project that needed some complex structural solutions. This commercial site in a residential setting consists of more than 30 Allan Block retaining walls varying in height with some exceeding twenty feet. The main walls of the project frame both sides of two land bridges with large culverts underneath. To manage the possible water flow below the walls, the flexibility of the culverts during construction and the traffic conditions on top of some of the walls, kept this project extremely interesting.
Plan
The original concept from the City of Beaverton included natural rock walls with a pillar or column feature to increase the aesthetics. With problems in the design concepts and initial estimates coming in way over budget, the general contractor started looking for different solutions for the project. He found Allan Block’s AB Collection on the internet and contacted the local manufacturer for assistance. Oregon Block worked with Allan Block Corporate and Columbia Machine to redesign the face of the block to create the pillared look desired by the city.
With their foot in the door, Oregon Block was able to take the project to the next level and provide a solution to the railing requirements above the wall as well. Using the new AB Courtyard Collection, the columns running through the wall were finished at the top with AB Courtyard posts to which the pedestrian railings were attached.
Design
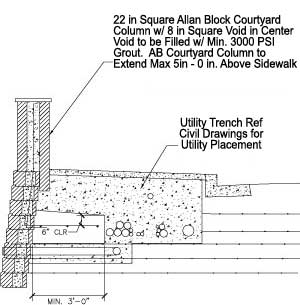
Figure 2: Allan Block Typical Section
Anytime segmental retaining walls are used in roadway applications, the design requirements are strict and this project was no different. Foundation soils located at the site were poor and with most of the walls having their footings located in wetland areas, a majority of the walls were designed as water applications with oversized granular footings to maintain adequate bearing capacity.
Another challenge during the design phase was managing the locations of the many private utilities required for the residential development. Locating them within the geogrid reinforced zone was not an option since future maintenance of the utility lines and the structural integrity of the Allan Block walls were required.
To solve this challenge, a utility trench was designed and located behind the wall to house the numerous private utility lines (Figure 2). The geogrid layout was modified to work around the trench, but still provided the structural requirements for the Allan Block wall.
Manholes and storm drains located behind the walls within the geogrid reinforced zoned needed to be considered as well. These drains were too large to simply place the geogrid reinforcement through the soil in the typical fashion so an alternative design was used. AASHTO required that the geogrid be fastened to all the manholes and storm drains (Figure 3). By connecting the layers of geogrid to the sides of the manholes the reinforced soil structure was maintained.
Build
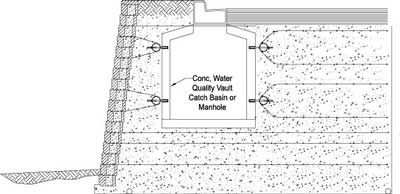
Figure 3: Manhole Detail
The construction of the Progress Quarry bridges needed to be well coordinated. The surveying team spent many hours laying out the placement of the walls and accounting for the block setback. This was especially critical since the design required the two walls to have a specific distance of space between them at the top for the traffic lanes.
During actual wall construction, the culverts designed were expected to flex as the land bridges were built around them. Each course needed to be placed and compacted simultaneously around the culvert to insure that the flex would be exactly the same allowing the block courses to match when the wall reached the top of the culvert. Concrete collars were cast to lock the blocks and culverts into place.
Even with the complex structural planning and site challenges that faced the project, the Progress Quarry Development turned out to be a huge success. With the beautiful AB Ashlar patterned walls, and AB Courtyard posts to accent the fencing, this functional site is a thing of beauty.