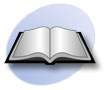
Print Case Study
Project Information
Name: McDonald's Fence
Union City, New Jersey
Product: AB Fence
Size: 200 ft (61 m) Long 22 ft (6.7 m) Maximum Height
Local Engineer: Allied Engineering
General Contractor & Wall Builder: Waiter Builder
Allan Block Manufacturer:
Clayton Block - Edison, New Jersey
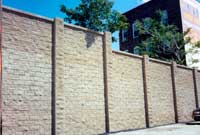
The fence was built to block out the loud traffic noise between a residential area and the McDonald's parking lot
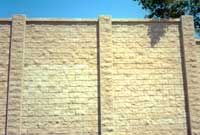
The AB Fence provides superior noise abatement, up to two times greater than the existing wood fence system
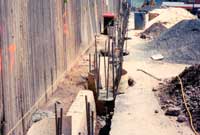
There was a layer of bedrock 3.5 to 7.5 feet (1 to 2.3 m) from the grade, making the foundation construction difficult
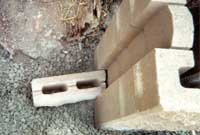
Post blocks were stacked, followed by the first row of panel blocks befor the horizontal rebar is laid
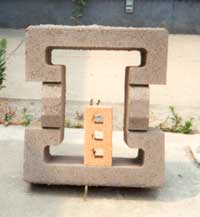
The new large post block had to be manufactured on a Comlumbia Machine at a separate facility and shipped into the jobsite
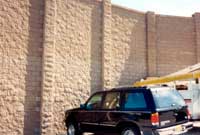
McDonald's Concrete Fence Project
"It is very important to let your customers know all of the products you sell. They may not need it today, but one never knows what will come in the future." states the Allan Block sales rep from Clayton Block. This was the case on a McDonald's Fence project located in Union City, New Jersey. Towering as high as 22 ft (6.7 m), the AB Fence was built to block out the loud traffic noise between a residential area and the McDonald's parking lot.
Plan
While discussing a retaining wall project with Waiter Builders, Clayton Block introduced the AB Fence system as another option for site solutions. Waiter Builders specializes in residential and commercial renovation as well as new construction. As luck would have it, they just happened to have another project in the works where an AB Fence application could be the solution.
Waiter Builders was working on a home remodeling project for the owner of several McDonald's Restaurants in area. The homeowner had mentioned that the Union City officials were requiring a fence to be put in to eliminate car headlights and traffic noise from interfering with the residents adjacent to the McDonald's parking lot.
The AB Fence system was perfect for this type of application. Not only could it provide superior noise abatement, up to two times greater than the existing wood fence system, it also has an incredible aesthetic style and is extremely durable. With all the information on the AB Fence system, the builder was able to discuss this solution with the owner of McDonald's. In no time, a design and estimates for the fence were under way.
Design
Allan Block Corporation worked along with Allied Engineering Associates to come up with a design for the concrete fence. A preliminary design was completed, based on assumed soil conditions that needed to be verified.
In the meantime, additional soil borings were conducted. It was discovered that there was a layer of bedrock 3.5 to 7.5 feet (1 to 2.3 m) from the grade. This meant that Allan Block and the Allied Engineering team needed a revised design. The soil conditions were better for the design, but made foundation construction a nightmare.
Drilling into the dense bedrock for post foundations was an expensive part of the project but reduced the pile depths and the amount of bond beams needed. After the final design, it was determined that the block fence would utilize a post spacing of 6.5 blocks (10.5 ft, 3.2 m) at the maximum height, and the pile dimensions would need to be 8 ft (2.4 m) deep with a diameter of 2.5 ft (0.76 m).
The panel sections required five #5 horizontal rebar in the bond beams, the post section required six #7 bars for vertical steel, and the piles required eight #7 bars for reinforcement. The final unit cost for the system was $34.50 per square foot including labor, materials and profit. The majority of the cost went to coring for the pile foundations. This alone cost over $35,000! This is why it is so important to determine what type of soil exists beneath the surface before determining labor costs on a project.
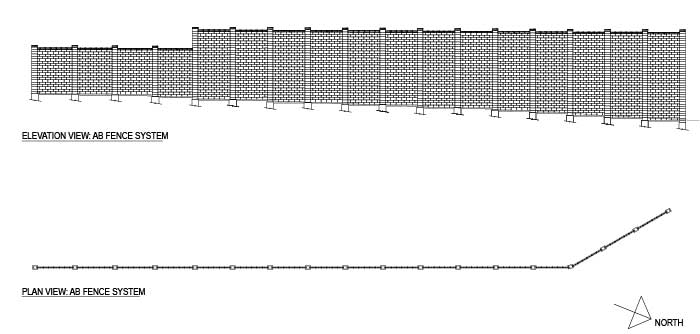
Plan & Elevation
Build
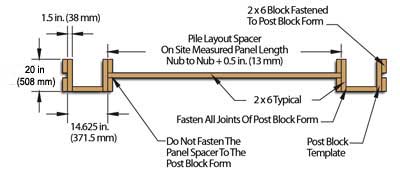
Spacing Jig
The new large post block was required to be run on a Columbia Block Machine. Since Clayton Block does not have this machine, the blocks had to be shipped in from another Allan Block manufacturer to the project site. When it arrived, an Allan Block Project Specialist was on site to help train the installers. The key to the construction was to first build a jig using the blocks that were delivered to the site. The diagram here is a drawing of the spacing jig that was built for this project. Once the jig was made, excavation began for the piles.
The vertical reinforcing bars were placed immediately into the poured piles. Once the piles were constructed and the base trench was excavated, they could now begin the post and panel construction.
First, two post blocks were stacked, followed by the first row of panel blocks. Then rebar was placed for the horizontal bond beam directly on the first panel block course. After the bond beam was laid, the second layer of panel blocks were placed on top of the first layer and the first two courses of post and panel block were filled with concrete grout.
Next, the installers placed more vertical reinforcement into the posts and continued this procedure until the top course was complete and caps were glued in place. In just fourteen working days the project was complete. The 22 ft (6.7 m) high project had a final count of 3,146 panel blocks, 473 half-panel blocks, 565 post blocks and 139 cap blocks.
This remarkable fence now acts a beautiful sound barrier to both the patrons of McDonald's and the residents of Union City New Jersey.