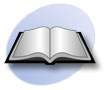
Print Case Study
Project Information
Name: Marston Slopes
Longmont, Colorado
Product: AB Fence
Size: 2,000 lineal ft(610 m)
General Contractor & Wall Builder: Slaton Brothers
Allan Block Manufacturer:
Basalite - Denver, Colorado
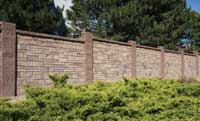
Due to a city ordinance, the fence could not exceed 8 feet (2.4 m) in height
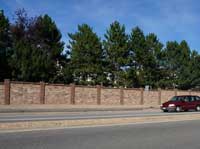
Not only did the fence reduce the vehicle traffic noise, but also gave the residents of Marston Slopes the security from the high volume roadway
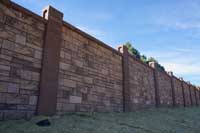
Both the panels and the final footing design required a 115 mph (185 kph) wind load
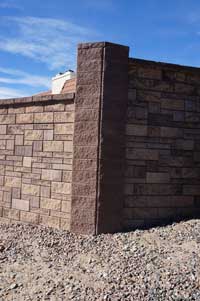
The versatility of AB Fence posts allows for clean mitering for non-ninety degree corners
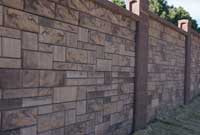
Ashlar pattern with the AB Fence system is a four block modular system that has a one-of-a-kind look that no other system can match.
Replacing an Old Wooden Fence
When old fences reach their design life, they begin to look run-down or may even be falling down. This was the case for Marston Slopes Residents in Lakewood, Colorado. The Marston Slopes Development had an old wooden fence that had been in place for years. Both Highway 44 and Highway 121 border the development and have steadily grown in traffic volume over the years, to a point where vehicle noise was quickly becoming a problem for the residents. The Marston Slopes Homeowners Association (HOA) looked for a solution to provide security, reduce traffic noise, and look appealing to the traffic driving by. Allan Block Fence stood out from the rest and exceeded all their expectations.
Plan
With an old wooden fence that stood only 4 feet (1.2 m) tall that had begun deteriorating to a point that it no longer provided the residents of Marston Slopes privacy or security, the HOA began researching different products to take its place. A fence that would meet each of the requirements that were set forth by the association, as well as be cost effective quickly set AB Fence apart from any precast concrete system. The HOA then needed to narrow down the options between AB Fence and another competitive system.
Both AB Fence and the other segmental system carry a unique installation quality that allows intermediate courses to be dry stacked with reinforced portions of the fence to hold up to wind loads. Sound abatement was relatively identical for the transmission loss for the two systems and they exceed the transmission loss for any wooden fence. Not only did both systems greatly reduce the vehicle traffic noise, but both gave the residents of Marston Slopes the security from the high volume roadway. Another requirement that the HOA had was to integrate an entry sign into the fence system which could be incorporated due to the modular system.
So what sets the two systems apart in order to make the decision?
Aesthetically, the Ashlar pattern with the AB Fence system once again set itself above other systems while remaining the cost effective choice for the project. The four block modular system gives the AB Fence system a one-of-a-kind look that no other system can match. Flipping around random blocks while following a pre-designed pattern, allowed both sides of the fence to experience the full aesthetic potential of the fence. Now that the HOA had made the decision on which system would be utilized for their situation, it was time to look at the most feasible design
Design
The AB Fence runs the entire length of the development which is located along two busy highways. The City of Lakewood and the HOA hired a professional surveyor to provide a detailed site survey so that the fence layout could maximize the yard space for the residences, while not encroaching on the right of way (ROW) for the roadways. A detailed site survey was very important for the (ROW), but multiple utilities ran parallel with the fence. The Allan Block Fence needed to be properly located so that a design that avoided buried utilities could be completed. In some areas the existing utilities dictated the required post spacing.
Due to a city ordinance, the fence could not exceed 8 feet (2.4 m) in height. The local engineer established that the panels required 3 bond beams located at the top, middle, and bottom of the panel height. Both the panels and the final footing design required a 115 mph (185 kph) wind load. Since a portion of the fence layout had utilities that ran along the path, an alternative footing design needed to be used. Although it was only a portion of the wall, a spread footing was used where pile depth intruded on the nearby utilities. After finalizing the design specifications for the project, it was ready to move on to construction.
Build
The local contractor, Slaton Brothers of Centennial, CO was awarded the project and began fence construction once the layout and design was finalized. Due to the utilities, more than 50% of the footings were hydrovac excavated so as to not hit a utility during excavation. Hydrovac excavation incorporates a large vacuum that allows excavation to take place without the risk of incidentally striking a utility line. Where the utilities ran close to the surface, Slaton Brothers used a concrete box around the utility lines to protect them during the fence installation and future construction.
A large grade change along the layout of the fence created multiple step ups in the fence while remaining a maximum of 8 feet (2.4 m) in height. The grade was gradual enough to place each of the step ups at the posts which saved time on the project while looking uniform throughout. The versatility of AB Fence posts allows for clean mitering for non-ninety degree corners and allows for easy panel height changes between adjacent panels.
Due to the lack of space for storage and the two major highways that ran parallel with the fence, pallets of block had to be brought to the site daily to keep the project moving forward. To save time on the project, the bond beams were constructed by pre-casting them off site which allowed a high quality production of the structural bond beams. Since the crew that constructed the bond beams were only focused on the pre-casting operation, the highest QA/QC could be met. The efficiency of offsite construction moved the actual fence construction at a quick pace. Each day, Slaton Brothers transported enough bond beams to the site to keep work moving forward while keeping the high traffic roadways open for commuters. The precast bond beams were lifted into place and the dry stack units placed by hand. This combination made panel construction very fast and efficient.
When nearly 2,000 linear feet (610 m) of fence had been installed, the final piece was the entrance sign for the development. Slaton Brothers had sent specifications to a precast company to create a concrete sign that nested perfectly into the AB Fence post pockets, requiring no mortar to secure it. The sign was created with a laser cut form which was painted a different color to give the sign a 3-dimensional look. The sign was set and secured in place of a dry stack section. This final piece to the project gives the residence of Marston Slopes a grand entrance to their development. The AB Fence system met all requirements from the HOA and the City of Lakewood while remaining the most cost effective and aesthetically pleasing fence system on the market.