Project Information
Name: Springs at Eagle Bend
Aurora, CO
Product: AB Classic & AB Fence
Size: 17,000 ft2 (1580 m2) of AB Classic & 8,500 ft2 (790 m2) of AB Fence
Wall Builder:
Slaton Brothers
Allan Block Manufacturer:
Basalite Concrete Products - RDenver, CO
AB Fence and AB Retaining Walls Solve the Many Site Problems
The Springs at Eagle Bend began development in late 2017 and is set to open during the Fall of 2018. Located in Aurora, CO just outside of Denver this luxurious apartment community will provide 280 apartment homes to individuals and families in the sought after Denver suburb. The resort-style community offers a large swimming pool, 24-hour fitness, community center, pet playground, spa and many other wonderful amenities. With multiple layout options to choose from, including 1, 2 and 3-bedroom options, the townhouse community will be sure to provide many residents with a home for years to come.
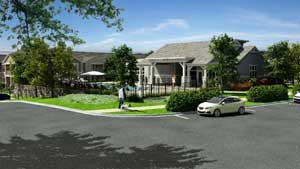
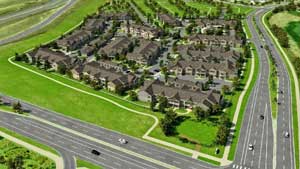
Plan
The Aurora area is home to many different corporations including IBM, Century Link and Centura Health. With multi-family living in high demand throughout the greater Denver area and specifically in the Aurora market, National Real Estate Developer, Continental Properties had a vision to create a destination apartment facility to help fill that need. Working with Civil Engineers from Martin/Martin Consulting Engineers in Lakewood, CO and Phillips Partnership Architecture and Engineering out of Atlanta, GA, Continental Properties was able to create a luxurious exterior and interior apartment complex similar to many other facilities they own throughout the country.
Local codes required noise abatement walls between the new Springs at Eagle Bend complex and the existing I-470 Expressway. The noise abatement walls would need to reach heights of just over 16 feet to perform as the required sound barrier and in that exact area a grade differential of up to 12 feet would need to be resolved as well. Multiple locations on the site had vast grade changes that would require an additional 12 retaining walls to correct grade differences of up to 14 feet. Continental Properties pulled together a team consisting of General Contractor, Dosters Construction and local AB Certified Contractor Slaton Brothers to help them solve the many site challenges. The goal was to find a common system to solve the various site challenges – Allan Block products manufactured by Basalite Concrete Products in Denver provided just the solution!
Design
Slaton Brothers hired SK Wall Design to complete the engineering for all walls onsite. Together, they were tasked with using their knowledge of various site solutions to solve the many challenges present at the Springs at Eagle Bend. Both were up for the challenge and the result was a perfect blend of AB Classics for the retaining walls and AB Fence for the noise abatement AND retaining wall portion.
Outside of two terraced sets of retaining walls correcting up to 14 feet of grade change, the retaining walls onsite were quite traditional. Designing a terraced retaining wall requires attention to detail and specifically to how all walls perform together. Due to the proximity of each wall (closer than twice the height of the lower wall/s) and subsequent loads the design would require burial and grid depth equivalent to the overall grade difference rather than the individual walls.
The real fun began with the noise abatement and retaining wall structure. SK Wall Design worked with the engineering department at Allan Block on the AB Fence solution for the Springs at Eagle Bend. The final design was different than a traditional application because of unique site conditions, but basic principles that have been used on various other AB projects helped solve the complex site.
No-Fines Concrete (NFC) has been used for 20+ years with Allan Block retaining walls and geogrid has been used for 35+ to reinforce soil behind segmental retaining walls. On the Springs at Eagle Bend project, both NFC and geogrid reinforced soil were used behind the AB Fence to ensure it would withstand the soil pressures. In most fence sections, SK Wall Designs created a CCS (Complex Composite Structure). A CCS is a single wall section with two distinctly different structures positioned one on top of the other. In this case and in most sections, you have NFC working within the bottom portion of the wall with geogrid reinforced earth sections directly on top (see section #1). The result created a structure with up to 5 feet (H) x 5 feet (D) of NFC with geogrid depths of up to 7 feet on top of the NFC to create the reinforced earth portions (see figure #1).
In addition to the use of NFC and geogrid, other unique characteristics to this design when compared to a traditional AB Fence included:
- Post rebar size #8 rather than the traditional #5 to add additional integrity to the structure (Figure #2).
- Rather than traditional two-course bond beams at the top and bottom (most common) the entire panel height reinforcing earth was constructed as a bond beam (in three-course lifts). This required rebar (#4) placed horizontally throughout the entire panel length and in between each course of block (see Figure #3).
- Stirrups, made of 9-gauge wire, were placed in every block core throughout the length of each bond beam and in three-course “lifts” as seen in figure #3.
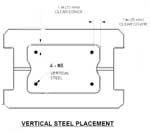
Figure 3
Build
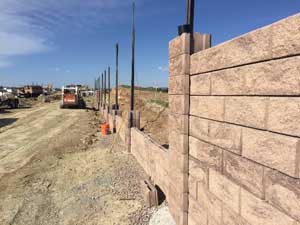
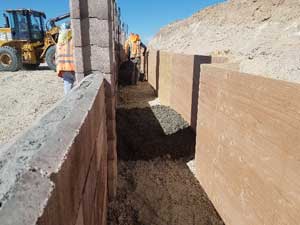
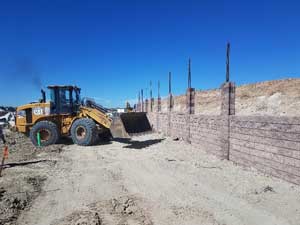
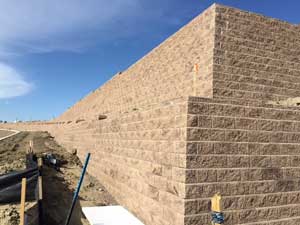
Slaton Brothers is an industry leading design and construction contractor providing solutions for many site challenges – retaining walls and sound walls are both part of those services. Due to the complexities outlined above, Slaton’s industry experience would be put to the test at the Springs at Eagle Bend. The challenges were going to be plentiful and included:
- Minimal room on the backside of the wall to work due to land restrictions.
- Challenges with local ready-mix suppliers who were not eager to provide the NFC material.
- Bedrock below the structure and specifically in areas where post footings were to go.
- Placement of the NFC along with the geogrid reinforced areas behind the wall to avoid bowing of the panel
Because it was challenging to access the area behind the wall, Slaton Brothers would have to fill behind the structure as they went up. General recommendation for a traditional AB Fence application with soil/aggregate behind the structure would see the entire fence built and then material placed behind it. Test panels were built to ensure no bowing would occur and field inspection was conducted to ensure the panels performed as intended – no problems due to Slaton Brothers attention to detail.
One of the biggest challenges was locating a ready-mix supplier to provide the necessary NFC. Because of the construction boom in the Denver area, concrete suppliers were very busy and providing a “specialty” mix was not something many were excited to do. Slaton worked with local companies on the mix design and eventually partnered with ready-mix supplier, Aggregate Industries who provided them NFC to meet SK Wall Design specifications.
Bedrock was encountered much closer to the surface than expected once pile construction began. Twenty-four-inch wide footings (SK Wall Design recommendation) were not going to be possible the entire depth of the post because of this. Slaton worked with SK Wall Design who reran calculations to determine 18-inch piles would be sufficient once bedrock was encountered. The original calculations were conservative because of soil parameters originally provided to them and having the ability to use an existing 18-inch auger with appropriate tip to drill through the bedrock saved significant time and money.
Scott Sothen with Slaton Brothers worked on the project from the onset with Continental Properties. He helped them navigate the waters to find the best solution for the site. “AB Fence worked well for us. We were using AB retaining wall products (AB Classics) for all other walls and it was a natural fit to keep the solution in the same family. With the ability to retain and provide sound abatement with one product that mirrored the site walls, it was an easy decision.”