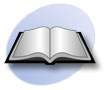
Print Case Study
Project Information
Name: CSX Intermodal Facility
Worcester, MA
Product: AB Collection
Size: 110,000 AB Units
Local Engineer: Clark Geotechnical, Woodstock, GA
Wall Builder: Vermont Lumber and Stone (VLS), Nashua, NH
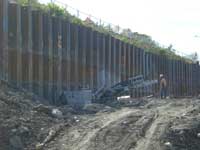
Sheet piling with a soil nail tie back system was used to reinforce the retaining wall.
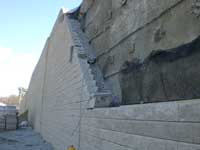
The project used multiple soil retention methods, including geogrid, soil nails, and sheet piling along with Allan Block
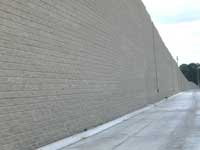
The final retaining wall was nearly one mile long with heights up to 35 ft. (10 m)
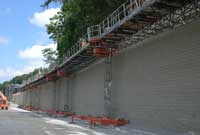
With virtually no access from behind the retaining wall a mobile hydraulic lift was used to safely move material during construction
Various Reinforcement Methods Make Difficult Project Possible
When CSX Intermodal Facility in downtown Worcester, MA needed to expand their property for new rail lines, multiple issues were encountered. With a local roadway at the top of the nearby hillside as well as utilities directly behind the proposed wall, this project presented numerous challenges to both the design and construction of the retaining wall. Incorporating the Allan Block segmental retaining wall system along with multiple reinforcement types would be investigated and applied to make this project an overall success.
Plan
The CSX Intermodal Facility is located in downtown Worcester, MA where space is limited for expansion. Initially, the plan was to use shotcrete and soil nails for the majority of the project and only a small portion of the walls would utilize geogrid reinforced segmental retaining wall block. Problems with the site soils and the aesthetics of the proposed wall did not allow the initial design to proceed. To solve the aesthetics challenge, the overall plan was changed from having 15,000-20,000 ft² (1,400-1,800 m²) of geogrid reinforced Allan Block wall to using Allan Block to face the entire wall including the geogrid and non geogrid reinforced areas. The resulting design used Allan Block to cover all 110,000 ft² (10,200 m²) of wall which satisfied the owner’s aesthetic requirements. Not only did the project encounter multiple design methods for construction, but there were also local utilities that ran behind the wall. Planning for these utilities dictated soil nail or sheet piling placement during construction of the wall. By incorporating multiple soil retention methods, including geogrid, soil nails, and sheet piling along with Allan Block as a facing allowed for a feasible and economical design that met CSX standards for quality and reliability.
Design
As with any project, the designer has many challenges that needed to be identified and overcome. In the case of the CSX project, not only were multiple reinforcement types deemed necessary in the planning stage, but additional areas of poor soils were found once excavation began. This again altered the direction of the final design and required additional areas of non-geogrid walls. Clark Geotechnical was hired to perform all retaining wall designs because their engineers were up to the challenges of this difficult site. In one of the areas of the CSX project, a roadway above and utilities behind the wall did not allow a conventional MSE wall to be used. Although soil nails with shotcrete could usually be used in these applications, poor foundation soils were found which would not allow for the proper bearing capacity requirements of the design. In this case, Clark Geotechnical decided to incorporate sheet piling with a soil nail tie back system. The tie backs allow the sheet pile wall to be taller and would not disturb the roadway or utilities on site. Although this method of construction is typically more expensive, it was the most viable option because the poor soils on site did not allow other retaining wall applications to be used. Soil nails with shotcrete could still be used in a large portion of the nearly 1 mile long retaining wall (1.6 km), primarily where conditions above the wall made excavation impossible and the wall height did not exceed the bearing on the foundation soil.
Clark Geotechnical had designed many Allan Block walls prior to this project, but none with such variety of design options. Typical construction for an Allan Block wall would be in a geogrid reinforced application, but for the CSX project, Clark Geotechnical had to come up with a wall connection detail in the non-geogrid areas that provided a seamless appearance from geogrid to shotcrete to sheet pile areas. They knew that using Allan Block as a facing to non-geogrid reinforced walls was common, but due to the tight time schedule, they came up with an alternate detail to the commonly used spreader bar option. First, they called for an additional coating of shotcrete to be placed over the sheet pile walls to provide a more uniform working surface. Then, they had steel eyehooks anchored to the walls at designed intervals and through the eyehooks they threaded commercial grade 7 wire cable which was tensioned to provide a connection point for the geogrid. Eyehooks and cable assemblies were installed at all geogrid layers from the bottom to the top of the wall sections. When the cables were installed, the Allan Block walls were constructed with geogrid layers coming out of the back of the walls which wrapped around the cable and then returned back into the wall at the next course up. The hollow cores of the Allan Block units and the void between the Allan Block wall and the shotcrete were filled with a clean washed gravel to provide easily compactable material for the installers and additional drainage for any incidental water in the area. Clark Geotechnical and CSX chose Allan Block , due to the very tight site constraints. The nearly vertical Allan Block units and innovative alternate cable connection method made the end product appear seamless from end to end of this nearly mile long, very diverse structure.
Build
VSL who was already a certified wall contractor through the Allan Block contractor training course, won the project. As with any railroad project, timing plays a major role in its success and this project was no different. The retaining walls had to be constructed first before any rail expansion could start. With virtually no access from behind the wall for most of the project length, VLS utilized a mobile hydraulic lift to safely move material during construction. Using their well-trained installers, the innovative hydraulic lift system, and their well-earned experience they installed an average of 1200 Allan Block units per day, even through the non-geogrid reinforced areas. The final wall was nearly 1 mile long (1.6 km) with heights up to 35 feet (10 m) which accounted for over 110,000 ft² (10,200 m²) of wall.
Although the project encountered multiple design considerations and the construction of the wall took special installation requirements, the retaining wall was a huge success. With proper design and construction of the CSX Intermodal Facility, the final wall exceeded the owner’s expectations and now stands on the downtown site.