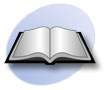
Print Case Study
Project Information
Name: Tallest Sound Barrier
So. Hackensack, NJ
Product: AB Fence
Size: 46,600 ft2 (4,330 m2)
Fence Builder:
Waiter Builders
Allan Block Manufacturer:
Clayton Block - Edison, NJ
AB Fence Solves the Problem for Required Tall Sound Wall
South Hackensack New Jersey is a heavily populated area bordering Teterboro Airport and only a short 10 miles (16 km) from downtown Manhattan New York. It has a mix of single family homes and multifamily apartment buildings and a very high population of light and heavy commercial business areas.
Plan
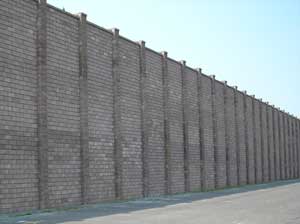
In one particular area the heavy commercial clashed with the local residential community due to 24 hour truck traffic and all night long property lighting. This situation became unbearable for the local homeowners and they sought a solution with the nationwide shipping company and ultimately with the city and then finally the courts. An agreement was found that the company would construct a sound wall to shelter the neighboring home from both the noise of the trucks and the overwhelming spread of the nightly site lighting. The company obtained an acoustical analysis from the highly regarded firm of Cavanaugh Tocci Associates, Inc. Their recommendation was that a 30 ft (9 m) tall wall was needed to accomplish both requirements. The company then sought input from local engineering firms to provide a possible solution for a wall that can reach heights of 30 ft (9 m). The engineering team at Allan Block Fence system for not only its strength but for its ease of construction. The shipping company was very pleased with the Allan Block Fence System proposal and quickly chose it for not only the benefits presented by Allied Engineering but when they saw the beauty of the finished, installed sample wall, it was their obvious choice.
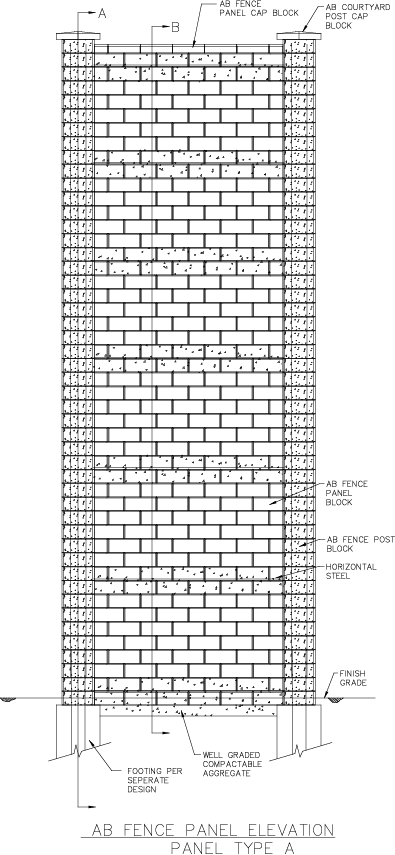
Design
Allied Engineering reached out to the Allan Block Engineering Department for assistance to fully understand the capabilities of AB Fence and together they decided to design the posts using the available Large Fence Post block for added flexural capacity. The AB Fence system stacks up using patented dry-stack post and panel blocks, with all blocks roughly 8 in. (200 mm) tall. The post blocks come in a standard 12 in. (300 mm) deep or the deeper 20 in. (508 mm) unit.
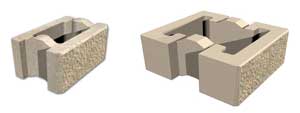
The AB Fence panels are designed and constructed separately from the posts using a combination of horizontal bond-beams and dry-stacked courses. The required wind pressure along with the desired wall height will dictate which post block is used. With the product information, Allied then proceeded with their design to best optimize the post spacing, vertical steel requirements and required number of two-course bond-beams in each panel.
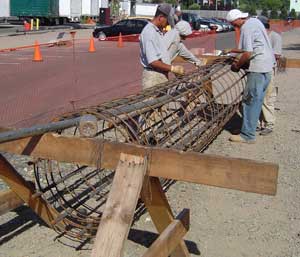
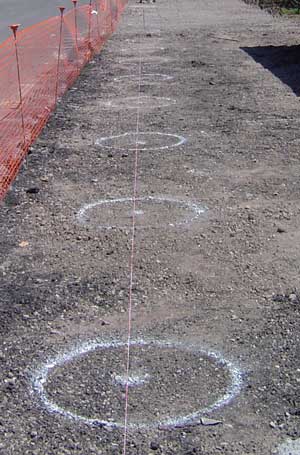
For the tallest 30 ft (9 m) panels there are 47 panel courses and 48 post courses to add a castellated appearance at the top. The maximum moment at the base of the post required 6 - #10 bars and #3 closed stirrups at 12 in. (300 mm) on center. Due to the amount of vertical steel within the post, there was not enough room for a traditional splice with the footing dowel bars. To solve this, Allied extended the height of the footing dowel bars into the post to a point where the rotational moment was small enough to allow a splice with a smaller diameter bar. The overall size of the fence and site soils did require Allied to design a large 30 in. (762 mm) diameter caisson to satisfy local building requirements. The panels required 7 – two-course bond beams which then provided for six dry-stacked sections consisting of either 5 or 6 dry-stacked courses each.
Despite the very large height for this project, Allied found the design process to be straight forward post and panel design. While the caisson footing tool added extra time to pull together, the taller posts and panels were simply a taller version of the easy to design Allan Block Fence System.
Build
Wiater Builders secured the project and worked with Allied to come up with a plan to start laying out the post footing for drilling and start auguring holes and overall project staging. During this time Wiater’s steel crew worked on the steel cages for the caissons. As with the design, the construction was very straight forward and Wiater’s crew had the experience building large projects. A couple of key staging parts to this project were to have the right equipment for drilling caissons, lifting the cages in place and a high quality scaffolding system. The scaffolding was very important as pallets of block were lifted and placed on the them for easy access by the construction crew.
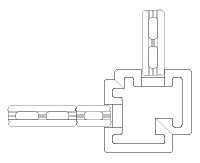
Mitred Corner
Some of the project was constructed during the cold New Jersey winter which required Wiater to follow standard cold weather construction techniques. See our tech sheet for a detailed discussion on cold weather construction. This AB Fence project had a number of inside and outside 90 degree corners which, when using the Large Post Block, requires mitering two standard Large Post blocks each course of the post. To save time building the corners, Wiater assigned two men to prep the block for the corners. They used the template Allan Block provided for cutting and prepped hundreds of right and left-hand units so they were ready to go when needed. For projects using the Allan Block Standard Post block, there is a separate 90 degree post block in the collection so mitering is not required for those projects.
This is the tallest AB Fence project at 30 ft (9 m) and was constructed in the early 2000’s, it continues to this day to provide the highest levels of function and esthetic beauty the customer required then and will well into the future.