Project Information
Name: Geosynthetic Reinforced Soil – Integrated Bridge System (GRS-IBS)
Hamilton Cty, IN
Product: AB Vertical
Size: 4 bridge projects completed
Wall Builder: Hoosier Pride Excavating, Springport, IN
Allan Block Manufacturer:
Reading Rock - Cincinnati, OH
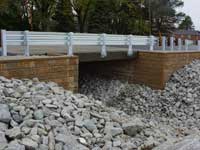
Two of the 4 GRS-IBS structures Hamiltion Cty, IN designed and constructed.
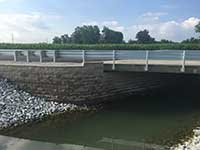
Hamilton County, Indiana Uses GRS-IBS to Overcome their Bridge Challenges
Geosynthetic Reinforced Soil – Integrated Bridge System (GRS-IBS) is being used to help solve the growing national demand to replace small, single-span bridges. The Federal Highway Administration (FHWA) has been pushing this design and construction method for over 10 years. GRS-IBS bridges provide a low-cost and durable solution that also requires less construction time. All the advantages Hamilton County Highway Department were looking for considering they had four bridge structures that needed to be replaced. Since the county was funding the project they were looking for the best way to remove and reinstall. The first bridge project they wanted to design was an 11-ft high by 24-ft wide (3.4 x 7.3 m) wood piled bridge structure that needed replacing.
Plan
When designs were considered for the bridge, the county was definitely looking at both the budget and the time required for construction. Therefore, conventional designs and standard driven pile systems were not the best solutions. By utilizing a GRS-IBS application, they were able to construct the new bridge in a matter of weeks instead of months. Additionally, they estimated that the GRS-IBS application would save Hamilton County over $500,000. Now that the county had the application to move forward with, it was time to start looking at the materials and design to ensure success.
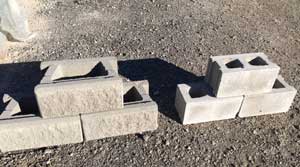
The use of Allan Block retaining wall units as the block facing provided the best solution when compared directly to the concrete masonry units (CMU) that were traditionally used for construction. In fact, the local Allan Block sales representative, Jill Fouts with Reading Rock, actually stacked up Allan Block and CMU units side by side for the design team to consider. The quality of a segmental retaining wall unit regarding durability and height tolerance far exceeds the traditional CMU. Faraz Khan with Hamilton County was quoted, “Versatility of Allan Block to adapt to our challenging project and meet the stringent specification requirement made it an ideal candidate.”
The FHWA does not have a current standard that requires using segmental retaining wall products as the face since the design methodology refers to using CMUs. Obviously, the reinforcing grids are tightly spaced so the connection to the geogrid or the actual pressure exerted on the back of the block is minimal, but there are very good reasons to use SRW units instead of CMUs:
- ASTM C1372 outlines the requirements for SRW units and provides minimum standards not only for block durability, but also dimensional tolerances. There is no mortar being placed between the blocks when constructing GRS-IBS structures. Therefore, the blocks need to have strict dimensional tolerances so they stack up and install evenly.
- For walls and abutments constructed in colder climates designers need to be aware of the freeze/thaw conditions and how the temperature influences block durability. SRW units have been used for retaining wall construction for almost 30 years. Each year the industry continues to push for block testing and higher durability standards in cold weather conditions. Producers are aware of these conditions and have SRWs tested accordingly. This testing is not normally done on CMUs.
- If you look at the original GRS-IBS designs they will often use a solid CMU or fill hollow CMUs with concrete when they are at or below the water level. The concern is that the block may crack if something impacts them. CMU block have a face shell thickness of about 1 inch (25 mm), compared to over 4 inches (100 mm) for an Allan Block. Therefore, solid blocks are not required below or at the water line. Using the same block throughout construction minimizes potential errors while keeping construction efficiency at the highest.
- Very often they will use a different color CMU block for the solid units to indicate if future erosion is taking place. However, this could be accomplished with Allan Block as well since multiple colors are available as seen in this picture from one of the Hamilton County project.
- Another reason why Hamilton County used Allan Block was that CMUs do not have a built-in shear mechanism. Allan Block’s front lip not only provides shear strength to each course of block, but helps create wall stability while aiding in installation. The front lip acts as a guide for the next course of block so the setback is built into the system and it takes the guess work out of the installation.
To incorporate the Allan Block into the GRS-IBS structure, Civil Design Professionals looked at the wall designs and provided the detailed construction drawings for Hoosier Pride Excavating, who was awarded the bid. Because of space limitations, they decided to utilize the AB Vertical to minimize the setback of the abutment structures. StrataGRS 4800 Geotextile, from StrataGrid Inc., was chosen as the reinforcing material since it is specifically designed for the GRS-IBS applications.
What was interesting about this project was how the actual bridge superstructure was constructed. Very often the bridge structure will incorporate precast concrete or even steel beams to span the distance between the block and grid abutments. However, for this project they utilized the existing wood piles from the old bridge to support the steel form work. The concrete deck was poured just beyond the bridge seat and once it was cured the steel supports and beams were removed. The piles were then cut off at grade and ultimately covered by rip rap.
Installation time was minimal which meant that reinstallation of the bridge was completed within budget and the strict time constraints of the project. In fact, here are some of the things they learned on the four bridge projects:
- The first two abutments used corners which they estimated added a full day to incorporate. The second two bridge projects rounded the abutments which saved time and enhanced the appearance.
- They enjoyed the competitive pricing since there are local contractors that are trained and understand how to build retaining walls. The crew size has typically been around 4 guys so it stays competitive since large and small companies can perform the work.
- Estimated that the GRS-IBS construction was 2-3 weeks faster than traditional bridge construction.
- They used red colored Allan Block units for embedment behind the rip rap to help indicate if scour issues start to occur.
All in all, these were very successful GRS-IBS applications that showcased future potential to the point that Hamilton County plans on replacing 2 bridges every year using this application. Daniel Alzamora with the Federal Highway Administration commented, “Hamilton county in collaboration with their design team completed an efficient design which allowed the contractor to be successful in constructing the bridges as planned. We will be sharing this experience with others nationally. Congratulations to Hamilton County for completing an excellent project.”
GRS-IBS applications do provide an economical solution to the countless bridges that need to be replaced. The FHWA indicates that 24% of the bridges across the country are in need of immediate attention. The hope is that more counties will utilize this technology and that designers will recognize the value of using SRW units as the facing element instead of CMUs.
For more information on GRS-IBS projects contact the Allan Block Engineering Dept.